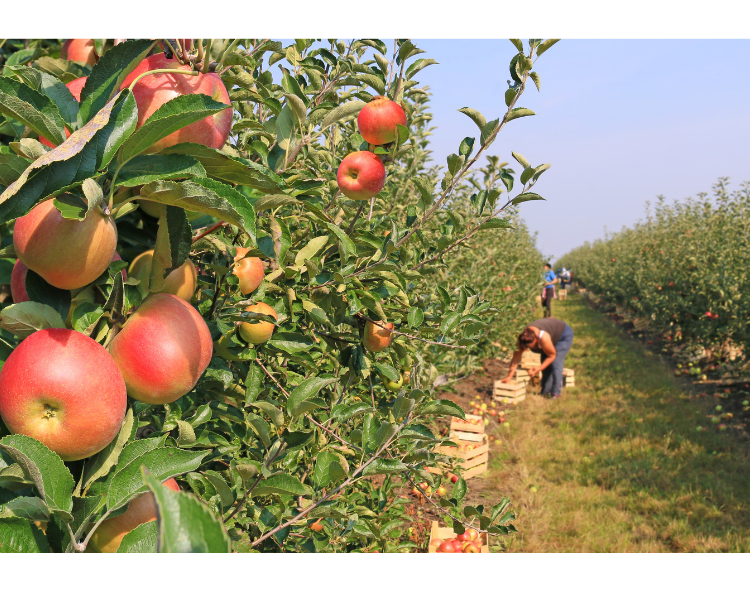
Growing Our World Class Industries
Over the last few years, I have been asked by aspiring NZ companies – ‘Who is world class?’ ‘What are we best at in NZ?’ Or even more insightfully, ‘what could we be best at?’
The current industries that have been resilient throughout COVID, where demand has remained strong and in some cases shown significant growth, provide some clues.
It is clear there is huge demand for our food produce, especially kiwifruit, apples, wine and of course the perennial meat and dairy. Over the years I have had the privilege to work in all of these industries.
The world sees us as a clean, green, high-quality food producer and, whilst we have areas for improvement, the horticulture industry is a shining example of this.
In the last decade we have seen significant growth in wine, kiwifruit and apples to name a few, with wine on a 24-year growth trend! There is significant potential to provide the world with high quality, high margin food and reinforce our global image.
Given this, it behoves all parties (employers, government, unions and other stakeholders) to work together to provide a roadmap to a green, profitable, and more sustainable industry.
COVID has heightened our awareness of the current challenges the horticultural industry faces and, to be frank, has been grappling with for a long time. Being a seasonal business, there are certain times of the year when there is a higher demand for labour.
This is typically around picking and packing (February through to June). Historically, many harvest operators have worked with the Ministry of Social Development (MSD), youth schemes, recruiters and so on, to fill the needs, with many a despairing operator/employer explaining that finding good people to fill roles was near impossible.
The issues were not so much about pay (as is the current discussion), but more about reliability (Friday night shift anyone? Saturdays? 6-day weeks?).
As a result, many shifts have a 50% turnout rate and are unable to operate properly. They’re costing the business money, are unproductive and have no viable alternatives.
Of course, pre-COVID, tourists were a labour source, but also problematic. They were trained, however, just as soon as they had enough money, many left to continue their travels. The employers would require full time trainers, working round the clock to train replacements, creating further costs and burdens.
Out of desperation, a few years ago, the industry looked at alternative labour sources to allow them to better meet their growing needs. Recognised Seasonal Employer (RSE) workers are reliable, hard-working and have since enabled industries to grow.
Now there are well-established processes and systems in place to provide housing, training, transport and other needs, whilst workers are away from home. With many RSE workers returning year after year, there is now continuity and a reduced training load.
Today the local market still needs to fill the employment gap. The issue though remains the same – the comparative productivity gap. If we need twice as many locals as RSE workers, then the profits will quickly disappear. Reliability aside, why are RSE workers more productive? Do they have better processes, methodologies, systems?
My observation is that the answer is ‘no’ to all of the above. RSE workers achieve greater productivity through sustained physical work, and experience gained over years, but they do not apply any different practices to the processes involved, versus local workers.
Over the years, I have observed the various grape, kiwifruit, apple, potato, carrot, onion and other producers, and noted the huge variability in the methods, systems and approaches taken, as to how the products are produced, picked, packed and despatched across different operations.
Imagine if we identified the most effective methods, and best use of the right technology, and applied them universally.
In some cases, by applying best practice, I have seen improvements of over 80% productivity by the same people in the same orchard and vineyard. Imagine the impact of this productivity improvement on the industry. Not only would labour productivity improve, but so would the orchard yield!
We are missing the forest for the trees (or orchards). All workers should be able to achieve the required productivity levels using defined best practice, to ensure the profitability of the industry, and to support the future anticipated growth. We have a real opportunity to create regional jobs and futures for many New Zealanders.
We need a government ministry to help fashion this roadmap, with stakeholders, to protect, nurture and grow strategic industries.
We need to do this by helping them to develop and implement best practices, to ensure higher levels of productivity and to enable the industries to pay above the living wage. This would be a more collaborative and strategic approach than shutting the gate and raising the cost.
I am committed, keen, and have been supporting this journey for over a decade. Join me.
By Ian Walsh, Managing Director - Intent Group NZ
If you'd like to meet and chat about how we can help you and your organisations on it's journey to World Class then get in touch with Ian on 027 534 9258 / email iwalsh@intentgroup.co.nz or local contact Antony Gibson on 021 161 9705
Images
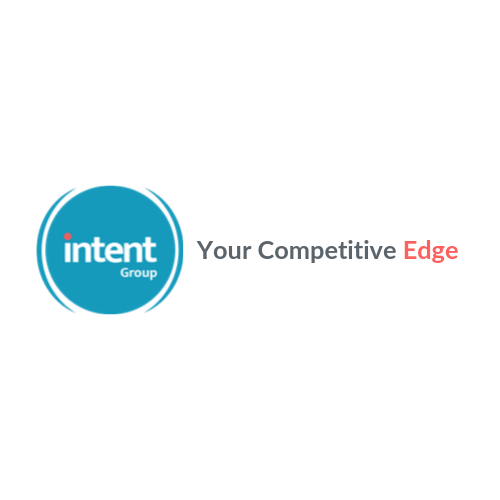
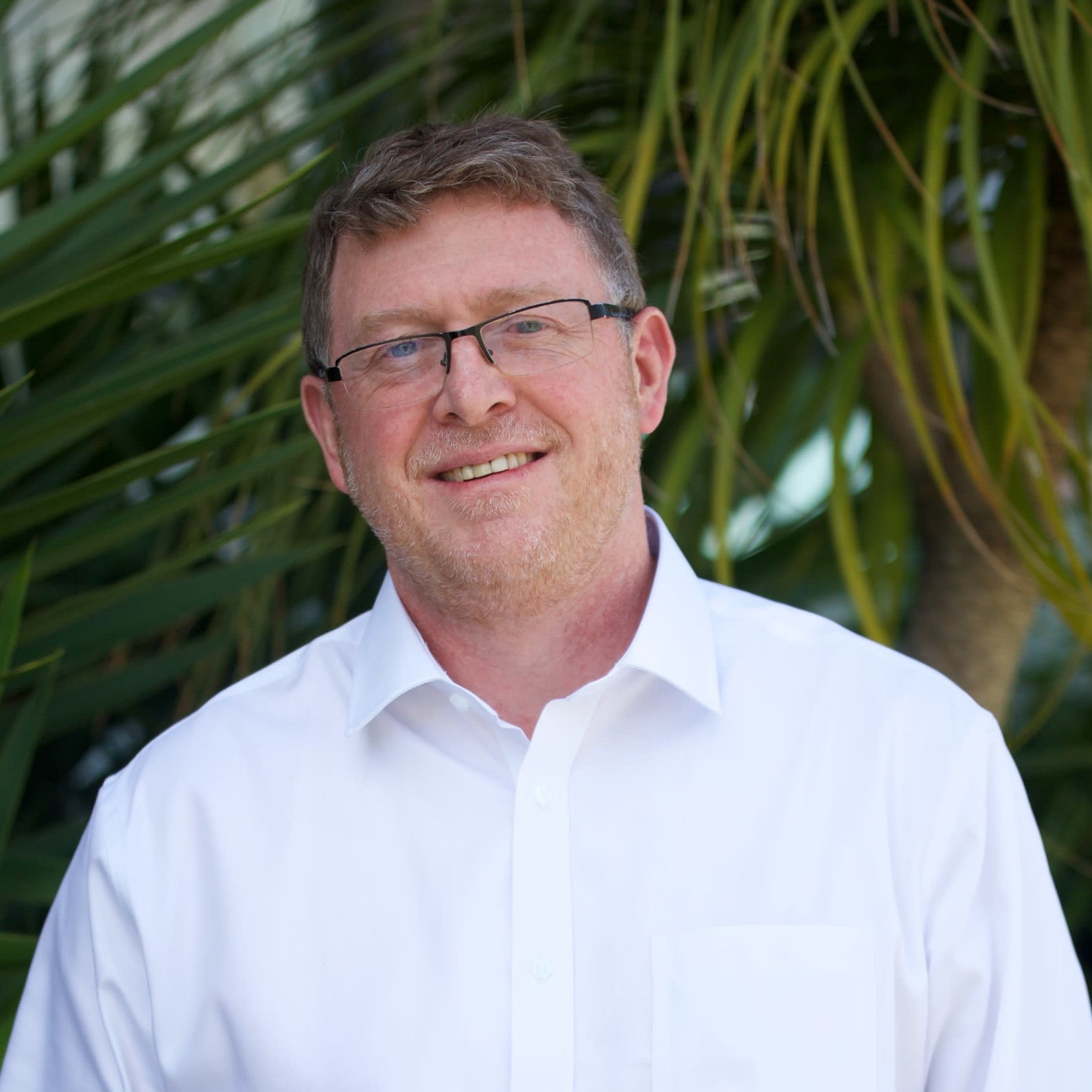
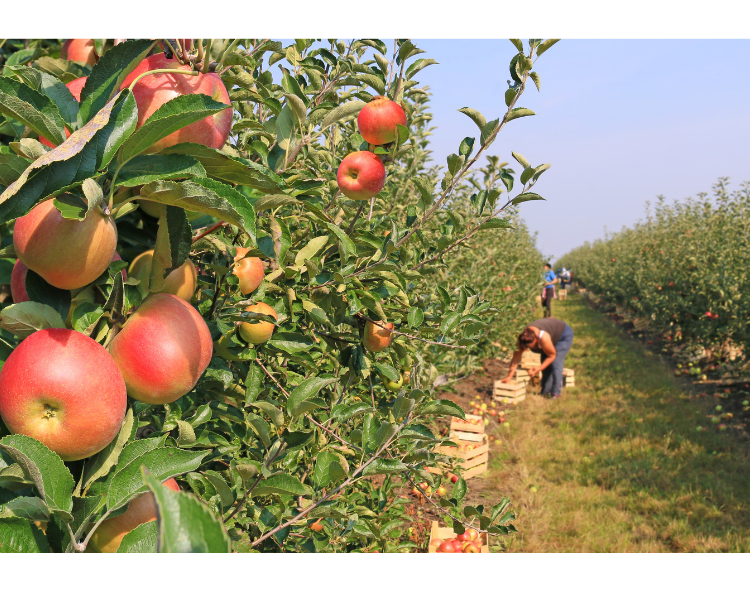