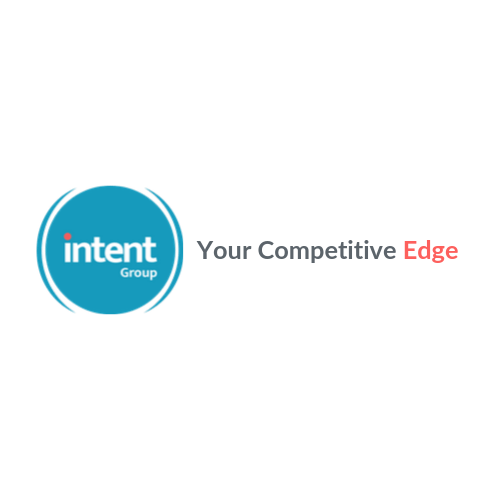
What gets measured gets managed!
I have recently visited a couple of companies and was surprised to see little, if any, data collection in real time. What’s more surprising is that many SMEs don’t even have good in-process data collection.
“Oh, that old chestnut”, I hear you say.
It is fundamental to any improvement program to have a good understanding of what is going on in your process. Yet here we are nearly in 2022 with a significant number of companies having little-to-no structured data collection to manage their processes. What’s even more criminal is that in this new technology-enabled Internet-of-Things (IoT), industry 4.0 stage, that there really is no excuse.
There are many off-the-shelf systems that can be installed, connected up and set going in just an afternoon! These aren’t expensive either – compared to the cost of manual collection, they pay for themselves many times over in a year, not only in the time saved, but also in the quality of information provided.
The critical thing with many processes is that many of the “losses” (time, quality defects, lost product and other wastes) are not easily visible as you move further and further from the process. The quality of the data available therefore becomes more and more critical to driving improvement efforts and maximising the best use of your critical resources. The best manual systems can achieve up to 95% accuracy, but most are operating in the 70-90% range and this require overhead to maintain. The issue with these systems is that the data that is usually not captured is the high-frequency short-duration stops.
Of course, the low-frequency long-duration stops (like mechanical breakdowns) everyone knows about because everything has stopped. The short duration, high frequency stops however, is more like death by a thousand cuts.
It seems barely worth recording when it takes just as long to record as it does to fix! The operator or process owner repairs the problem, resets the process and away we go until it happens again!
And again, and again, and again…
Because manual systems are so poor at capturing this data, it’s not prioritised and therefore not addressed, even becoming accepted as “just the way it is”. The problem with this is that because these stops are recurrent, they are easy to observe and usually easy to fix. The benefit for fixing them is received almost immediately, so these are the problems you want to address first.
Empirical data gives you the case for tackling these issues and getting support from the affected teams to fix them, which in turn makes the repair process easier and more impactful, as well as giving it the priority it deserves.
Information is critical to give visibility to plant performance and priorities. I went to a plant in the UK where one process stopped 455 times in an 8-hour shift and was the bottleneck on the whole process – that’s nearly once per minute. The operator, intervened every time to lift a fallen bottle, replace the guard and hit the restart. No downtime was recorded for the entire shift. Nothing was done as the management were unaware because there was no downtime recorded due to this conveyor. The operators were frustrated, and this had been going on for 4 years. It took just 2 days to solve.
Another critical area to have good data around is the process running speed. Speed loss is invisible downtime as the process is still running everything looks ok, but if you are going at half speed your biggest loss is process speed. This can vary depending on the process, human or mechanical systems and product mix. Every business, however, should know what each process’s potential is to measure their true efficiency and identify gaps. Without this visibility you will not know why the process has been slowed down and what problem is the causing the team to do this.
All of these losses are very hard to address without good data capture systems in place reporting on a shift-by-shift basis at minimum, and real-time at best. Of course, simply just having the data will not make your business world class by itself, but having no data will guarantee that outcome.
As the old axiom says, what gets measured gets managed.
If you want to know more about some of the available solutions, we are happy to share our experience. Drop me a line. iwalsh@intentgroup.co.nz or contact our local consultant Darren Ward on 0212277680
Images
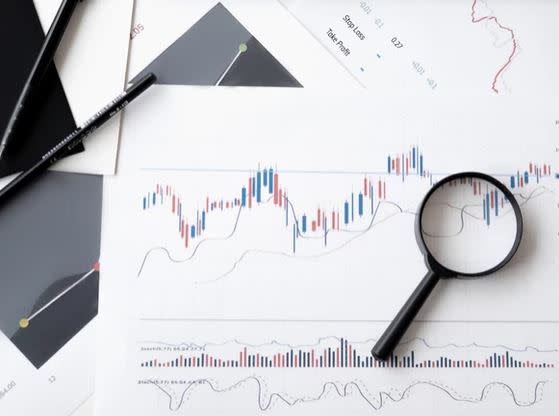
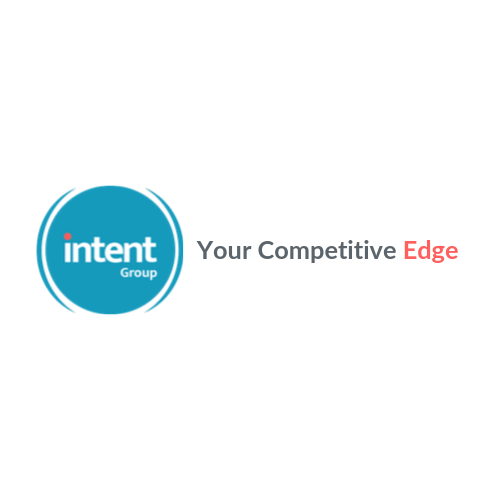
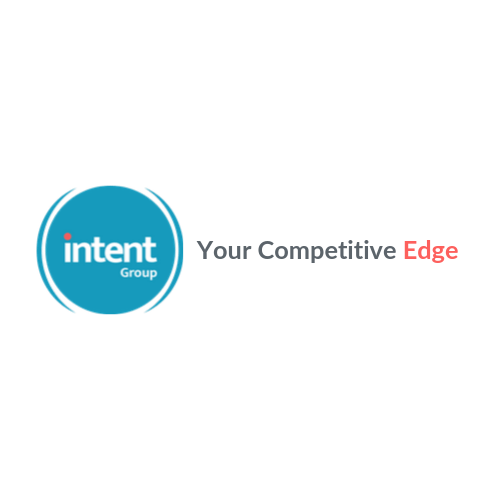